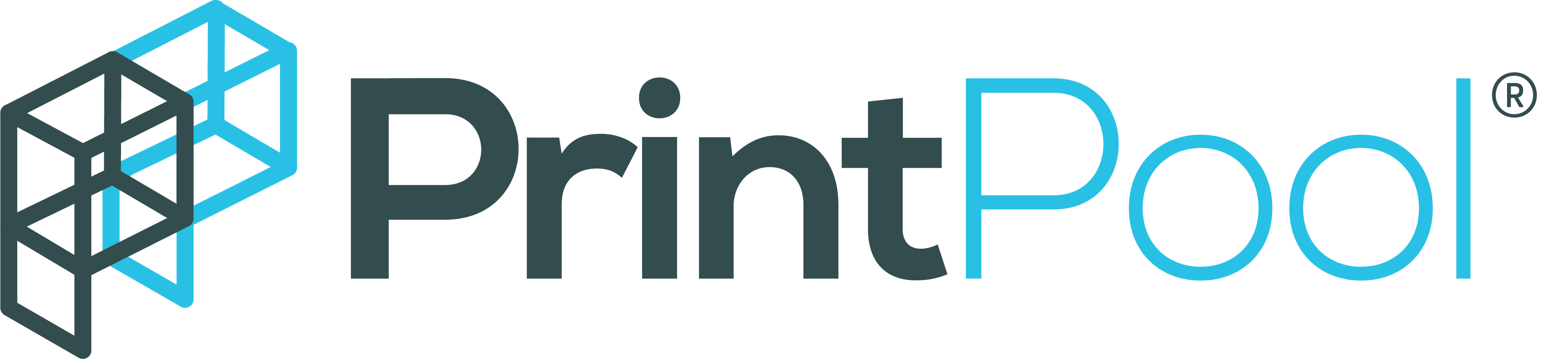
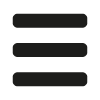
SLS 3D printing produces excellent parts that can withstand shocks, high temperatures, and chemical exposure. No support materials are required either! The largest possible part size is 165 × 165 × 300 mm.
Hole Size
> 1.5mm
Overhangs
N/A
Wall Thickness
> 1.5mm
Emboss/Engrave
> 1.2mm width
> 0.8mm depth
Bridging
N/A
Clearance
0.15mm Tight
0.25mm Loose
SLS is well-suited to producing medium to large production runs of components for end-use. Reach out to us to discuss whether SLS 3D printing would be a good alternative to injection moulding for your project.
Our selective Laser Sintering (SLS) materials benefit from the unrestricted, and support-free, design freedom that only powder additive manufacturing can really offer. SLS produces parts with excellent dimensional accuracy, and also offers very good isotropic mechanical properties.
This material offers the greatest design freedom as it prints support-free. Good for production runs, as it is more scalable than other materials.
SLS NylonPrintpool offers a range of professional 3D printing services to engineers and product designers across the UK. We provide a world-class additive manufacturing service, and unlike many competitors, are happy to discuss your application in detail and answer any questions you might have. We will sometimes recommend small design changes if we think that it will improve the end result!
Selective Laser Sintering (SLS) involves using a carefully controlled laser to carefully sinter (rather than melt) a fine polymer powder. Like with many other additive methods, each component is built up in layers, as the laser will sinter one part of the cross-section of the design at a time. After a layer is freshly sintered, additional powder is added on top, in a very thin layer. When the laser sinters the next cross-section, the new material in the layer below and above also sinter together - and so a full component builds up.
Once the print has finished, the solid parts are separated from the unsintered powder. The loose powder is sieved and mixed with around 30% fresh plastic powder, before it can be used again. SLS is one of the most suitable additive manufacturing processes for mass-producing functional parts, as no support material is required. Instead, the unsintered powder surrounds the parts in the print volume, naturally supporting every surface perfectly.
SLS parts have a distinctively textured appearance, but as the surface finish is so consistent - SLS is very suitable for cosmetically important parts. Further surface treatments are also possible for SLS nylon - dyeing, smoothing, painting, media tumbling and bead blasting. When smoothed or coated, SLS parts can be made waterproof.
The main advantages of Selective Laser Sintering (SLS) 3D printing are the geometric freedom that the process provides. Not needing to account for support structures make the design process far easier. When post-processed, the finish can come very close to injection moulded parts, and material properties of nylon are excellent for many engineering components.
Production runs are possible, with hundreds of thousands of parts produced, as well as functional prototypes. Many parts can be post-processed at the same time, making this process very efficient.
SLS 3D printing is an excellent way to produce the complex topologies that come from generative design or lattice structures, that can't be made with traditional manufacturing techniques. Nylon 12 has very good thermal stability, and works well for durable parts and 'looks-like' prototypes alike.
SLS mechanical properties are more isotropic than FDM or CFR processes, and are much better than the stereolithography (SLA) process.
SLS technology doesn't require support structures, which means SLS can do things other 3D printing processes can't do.
It is possible to arrange multiple parts in 3D space, and submit all of them as a single STL file for printing. This can sometimes save you money.
The selective laser sintering (SLS) printing process is far more industrial than other techniques. This technology is not well suited for anything but a production environment, and so isn't as widespread as FDM printing or resin printing. Nylon powders, in their unsintered state, are also dangerous, both as an explosive risk and an inhalation hazard. Of course - ordering SLS parts from us means you won't be exposed to those risks!
Parts printed from SLS materials also have a powdery texture, which may not be suitable for some applications. If not carefully designed, nylon prints are susceptible to warping, caused by different rates of cooling across thicker and thinner areas of the component - making the process unsuitable for some designs.
Designing for the selective laser sintering process is fairly straightforward. The main concept to bear in mind is that large flat objects, or shapes with very variable thickness, are prone to thermal stresses which can cause warping. This usually accounts for the majority of the dimensional inconsistencies between the CAD model and the physical part on larger pieces.
We advise trying to remove sharp edges from your parts, as these can encourage stress concentrations to form, which will weaker your final 3D print. Also, no area of the design should be thinner than 1mm, as this may not build properly. We have further, more detailed advice in our resources pages.
In 1986, Carl R. Deckard filed a patent of a Method and apparatus for producing parts by selective sintering. This patent was commercialised by DTM until they were acquired by 3D Systems in 2001. 3D Systems maintained an incredibly dominant position in the market for SLS printers, alongside EOS, a major competitor.
As with many other forms of additive manufacturing, in recent years smaller, desktop sintering machines have been released onto the market, most notably by Sintratec, SinterIt, and Formlabs. Each of these companies has released desktop SLS machines in the past five years that produce high quality parts, and are much cheaper than the larger industrial machines offered by their more established rivals. This competition is a good thing, as the competition will improve the quality of machines available.
No, its just a little different. Although both powder based processes, MJF parts are a little less accurate, but have the advantage of being naturally waterproof. SLS printing is higher resolution, and better suited to certain types of designs.
Unlike some other technologies, SLS 3D printers produce parts that are entirely solid. Parts are also more isotropic (the same mechanical properties in all directions). Parts with large solid sections should usually be hollowed in CAD software to save money and reduce thermal warping, however.
We will always remove the loose powder, and gently blast your components with unsintered nylon powder, to improve the surface finish. When you receive your print, no further finishing should be needed for the vast majority of applications, but dyeing and smoothing is possible.
Choosing what process to use for each print is critical. Generally 'blockier' parts, with a clear flat surface upon which to build, will be better for CFR, and more organic shapes with smooth curves should be sent for SLS. SLS is also more appropriate for large volumes of the same part.
If you wish to send multiple design files, please put them in a zip folder first! Our website will only accept a single file.
If you require 3D scanning services, please include a picture of the object you need to be scanned.